“尚经理,广州江铜能否尝试生产一种1.6MM全新规格的铜线?有一位东南亚客户急需120吨进行试单,并要求一周内完成装货。如果试用满意,他们将与我们签订长期稳定的合作协议。”11月,公司国际事业部向广州江铜提出了一项紧急且充满挑战的产品需求。
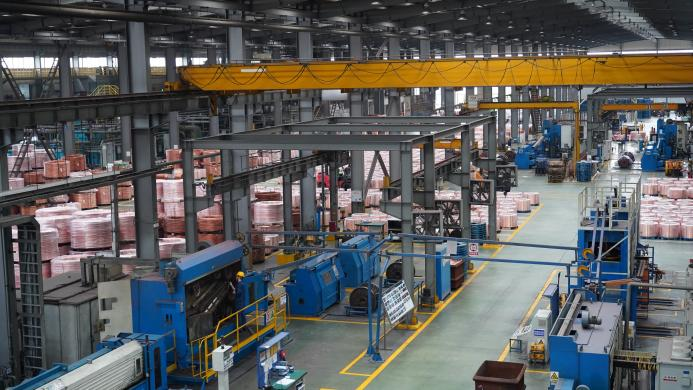
全新规格,意味着这是广州江铜从未涉足过的领域,没有任何现成的测试经验可供参考。一周内完成开发,更是一个看似不可能完成的任务。然而,广州江铜深知这一订单对于公司国际市场开拓的重要意义,当即召开了一场紧急专项会议。
会上详细列出了产品开发面临的三大难题:1.6MM规格产品超出设备加工极限、工艺参数缺失以及产能紧张。每一个问题都如同横亘在成功路上的巨石,让人倍感压力。
面对这些艰巨的挑战,广州江铜生产团队并没有退缩。他们针对每一个问题,逐一分析,寻找可行的解决方案。在生产工艺上,他们决定在现有基础上进行探索,通过调整模具压缩比来拓宽加工范围;在工艺参数上,他们搜集现有客户的数据进行参照比对,同时结合厂内设备进行测试;在产能问题上,利用峰时电进行试产,确保客户提货需求。
经过不懈努力,终于在两天后成功生产出两轴试制品,并通过了排线测试。然而,就在大家以为可以松一口气的时候,新的问题接踵而至:铜线表面出现了氧化斑点。
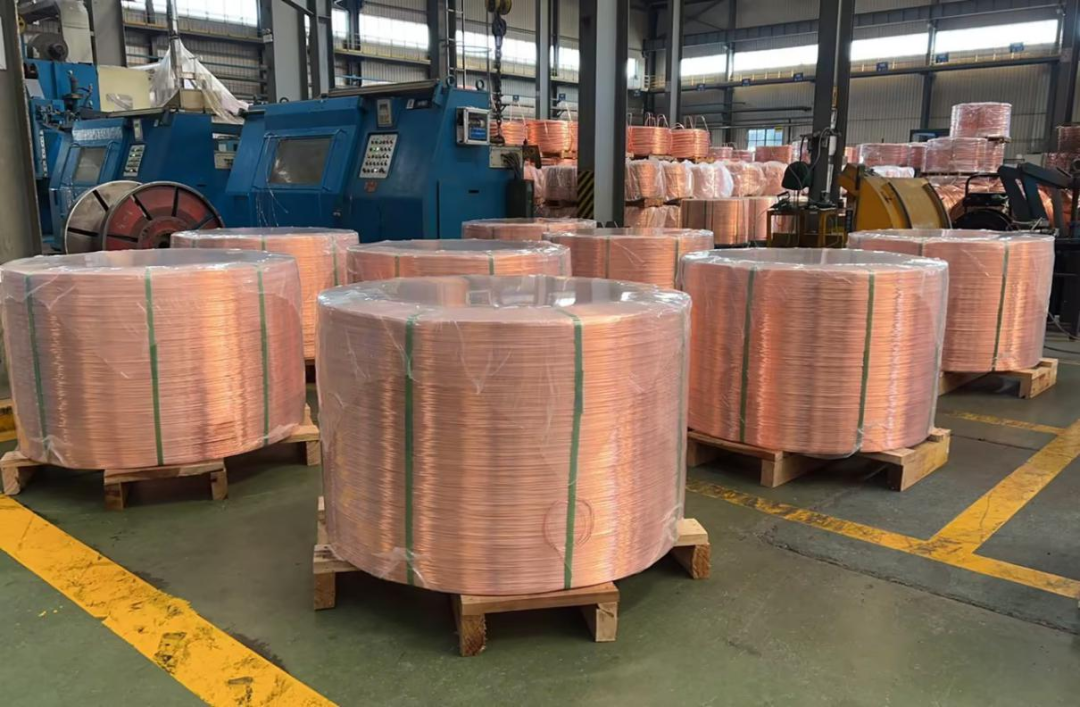
团队再度陷入严峻挑战之中。经过细致入微的分析,他们确认问题的根源在于1.6毫米规格铜线的细小线径,这使得排线布局极为紧凑,进而阻碍了退火过程中余热的释放以及空气中水蒸气的有效驱散。尽管倾尽全力寻求改善,但成果依旧不显著,加之交货期限日益逼近,团队正承受着前所未有的巨大压力。
恰在此时,一个不经意的瞬间为团队点亮了希望之光。一名车间员工正使用高压气管吹扫铜板的场景,意外地启发了团队负责人的灵感。“既然我们无法在后续环节中彻底排除水分,何不尝试在收线前就将其消除呢?”这一念头迅速转化为行动。团队决定对退火机的出口吹干模块进行革新,通过提升空气压力并优化防水垫片的设计,来显著增强吹干效能。经过一系列改造措施的实施,氧化斑点问题得到了明显改善,车间也成功开始了批量生产。
“线径最小公差0.01MM,满足客户±0.02MM的要求,伸长率33%-34%,达标。”
功夫不负有心人,经过检测,1.6MM全新规格产品检测数据得到客户高度认可,也标志着广州江铜成功开发出了新产品。
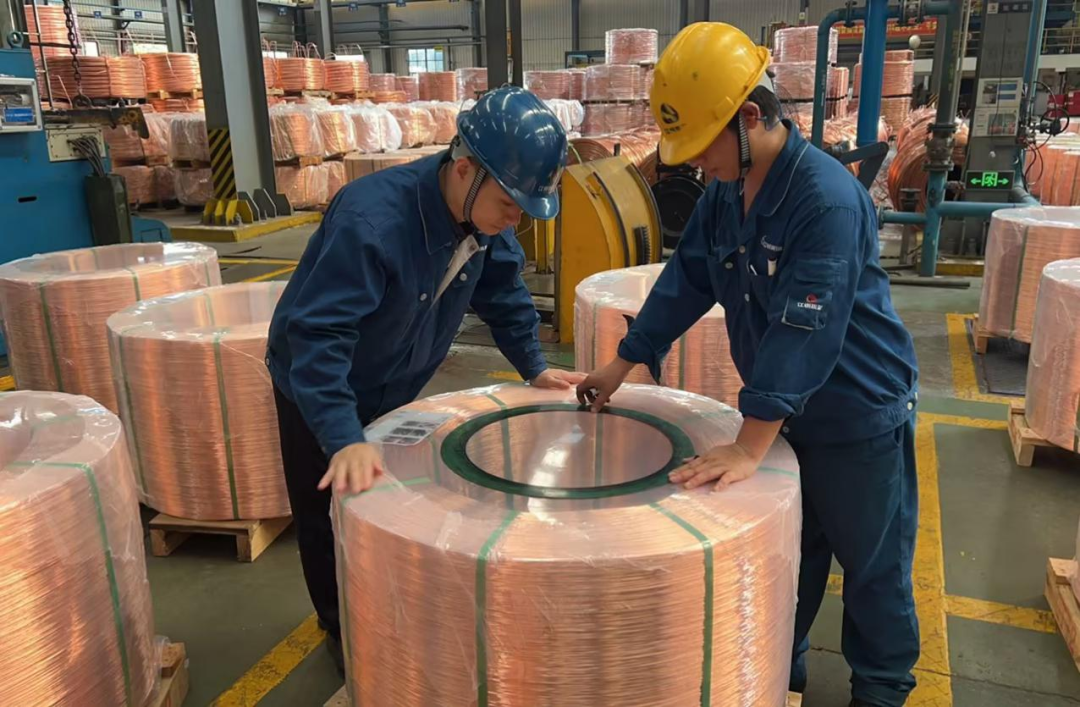
“以客户为中心”,始终是公司坚持的行动指南。未来我们也将继续秉持这一理念,不断推动技术创新和产品升级,为客户提供更加优质的产品和服务。